Robotic DR implementation and AI establish in Oil and Gas project
Tracks
Energy
Wednesday, October 23, 2024 |
11:30 AM - 12:00 PM |
207/208 - Technical Session |
Details
In the Oil and Gas industry, managing an extensive volume of over 300,000 films within a single mega-sized project is a formidable challenge. Traditionally, film radiography testing (RT) has been employed for quality assurance during post-weld inspection in piping construction. However, this process involves time-consuming tasks such as changing, handling, and developing film. To address these inefficiencies, we propose the adoption of modern robotic direct digital radiography (DR) including practical experience.
Our study demonstrates that DR significantly enhances workflow efficiency. The shorter exposure time required for DR compared to film RT streamlines the inspection process. Moreover, the elimination of manual film handling and development reduces labor-intensive efforts. Notably, DR is also an environmentally friendly technique, aligning with sustainable practices in the industry.
This presentation explores environmentally conscious DR methods. These advancements offer a promising avenue for improving inspection practices, especially in large-scale projects may require 300,000 films and above. DR does not need air-conditioned containers for storage films due to the direct digital process. We aim to revolutionize non-destructive testing while minimizing environmental impact. Also, DR introduces digital transformation and new working standards in the industry.
X-ray and gamma-ray based defect detection is a key technology in industrial pipe weld inspection in the Oil and Gas industry. With the integration of artificial intelligence (AI), modern direct digital radiography (DDR) systems have the potential to revolutionize the efficiency and accuracy of the pipe weld inspection process compared to established analogue film or film scanning with advantages. Fully direct digital imaging systems with automated robotic motion- and image acquisition controls and auto-stitching capabilities allow efficient image review workflows for the end user while maintaining access to raw data for machine learning (ML) analysis and documentation purposes. Through traditional machine learning techniques trained on large datasets of weld images, artificial intelligence can detect several types of defects, flaws or more generally weld discontinuities such as porosities, lack of fusion, and other elongated indications. The AI is used to help detect and classify suspicious discontinuities in the welds to maximize the process quality. However, the final decision to either reject a defect, or accept it with indications or treat it as an AI false positive – all according with ASNT, ISO or other applicable international standards – shall be made by a human expert. We propose a continuously learning AI that follows a transfer learning approach based on a distributed, multi-tenant online cloud infrastructure to collect human feedback and continuously gather knowledge to improve the AI.
By using the AI, a new working platform would be launched and provide remote real-time inspection by all workforce of the industrial professionals. It would reinforce overall work efficiency and quality, will lead further digital transformation by using the data stored in server of the images of DR with the results of interpretation.
Our study demonstrates that DR significantly enhances workflow efficiency. The shorter exposure time required for DR compared to film RT streamlines the inspection process. Moreover, the elimination of manual film handling and development reduces labor-intensive efforts. Notably, DR is also an environmentally friendly technique, aligning with sustainable practices in the industry.
This presentation explores environmentally conscious DR methods. These advancements offer a promising avenue for improving inspection practices, especially in large-scale projects may require 300,000 films and above. DR does not need air-conditioned containers for storage films due to the direct digital process. We aim to revolutionize non-destructive testing while minimizing environmental impact. Also, DR introduces digital transformation and new working standards in the industry.
X-ray and gamma-ray based defect detection is a key technology in industrial pipe weld inspection in the Oil and Gas industry. With the integration of artificial intelligence (AI), modern direct digital radiography (DDR) systems have the potential to revolutionize the efficiency and accuracy of the pipe weld inspection process compared to established analogue film or film scanning with advantages. Fully direct digital imaging systems with automated robotic motion- and image acquisition controls and auto-stitching capabilities allow efficient image review workflows for the end user while maintaining access to raw data for machine learning (ML) analysis and documentation purposes. Through traditional machine learning techniques trained on large datasets of weld images, artificial intelligence can detect several types of defects, flaws or more generally weld discontinuities such as porosities, lack of fusion, and other elongated indications. The AI is used to help detect and classify suspicious discontinuities in the welds to maximize the process quality. However, the final decision to either reject a defect, or accept it with indications or treat it as an AI false positive – all according with ASNT, ISO or other applicable international standards – shall be made by a human expert. We propose a continuously learning AI that follows a transfer learning approach based on a distributed, multi-tenant online cloud infrastructure to collect human feedback and continuously gather knowledge to improve the AI.
By using the AI, a new working platform would be launched and provide remote real-time inspection by all workforce of the industrial professionals. It would reinforce overall work efficiency and quality, will lead further digital transformation by using the data stored in server of the images of DR with the results of interpretation.
Speaker
Mr Teruaki Sano
Assistant Technical Group Manager
JGC Corporation
Robotic DR implementation and AI establish in Oil and Gas project
Presentation Description
In the Oil and Gas industry, managing an extensive volume of over 300,000 films within a single mega-sized project is a formidable challenge. Traditionally, film radiography testing (RT) has been employed for quality assurance during post-weld inspection in piping construction. However, this process involves time-consuming tasks such as changing, handling, and developing film. To address these inefficiencies, we propose the adoption of modern robotic direct digital radiography (DR) including practical experience.
Our study demonstrates that DR significantly enhances workflow efficiency. The shorter exposure time required for DR compared to film RT streamlines the inspection process. Moreover, the elimination of manual film handling and development reduces labor-intensive efforts. Notably, DR is also an environmentally friendly technique, aligning with sustainable practices in the industry.
This presentation explores environmentally conscious DR methods. These advancements offer a promising avenue for improving inspection practices, especially in large-scale projects may require 300,000 films and above. DR does not need air-conditioned containers for storage films due to the direct digital process. We aim to revolutionize non-destructive testing while minimizing environmental impact. Also, DR introduces digital transformation and new working standards in the industry.
X-ray and gamma-ray based defect detection is a key technology in industrial pipe weld inspection in the Oil and Gas industry. With the integration of artificial intelligence (AI), modern direct digital radiography (DDR) systems have the potential to revolutionize the efficiency and accuracy of the pipe weld inspection process compared to established analogue film or film scanning with advantages. Fully direct digital imaging systems with automated robotic motion- and image acquisition controls and auto-stitching capabilities allow efficient image review workflows for the end user while maintaining access to raw data for machine learning (ML) analysis and documentation purposes. Through traditional machine learning techniques trained on large datasets of weld images, artificial intelligence can detect several types of defects, flaws or more generally weld discontinuities such as porosities, lack of fusion, and other elongated indications. The AI is used to help detect and classify suspicious discontinuities in the welds to maximize the process quality. However, the final decision to either reject a defect, or accept it with indications or treat it as an AI false positive – all according with ASNT, ISO or other applicable international standards – shall be made by a human expert. We propose a continuously learning AI that follows a transfer learning approach based on a distributed, multi-tenant online cloud infrastructure to collect human feedback and continuously gather knowledge to improve the AI.
By using the AI, a new working platform would be launched and provide remote real-time inspection by all workforce of the industrial professionals. It would reinforce overall work efficiency and quality, will lead further digital transformation by using the data stored in server of the images of DR with the results of interpretation.
Our study demonstrates that DR significantly enhances workflow efficiency. The shorter exposure time required for DR compared to film RT streamlines the inspection process. Moreover, the elimination of manual film handling and development reduces labor-intensive efforts. Notably, DR is also an environmentally friendly technique, aligning with sustainable practices in the industry.
This presentation explores environmentally conscious DR methods. These advancements offer a promising avenue for improving inspection practices, especially in large-scale projects may require 300,000 films and above. DR does not need air-conditioned containers for storage films due to the direct digital process. We aim to revolutionize non-destructive testing while minimizing environmental impact. Also, DR introduces digital transformation and new working standards in the industry.
X-ray and gamma-ray based defect detection is a key technology in industrial pipe weld inspection in the Oil and Gas industry. With the integration of artificial intelligence (AI), modern direct digital radiography (DDR) systems have the potential to revolutionize the efficiency and accuracy of the pipe weld inspection process compared to established analogue film or film scanning with advantages. Fully direct digital imaging systems with automated robotic motion- and image acquisition controls and auto-stitching capabilities allow efficient image review workflows for the end user while maintaining access to raw data for machine learning (ML) analysis and documentation purposes. Through traditional machine learning techniques trained on large datasets of weld images, artificial intelligence can detect several types of defects, flaws or more generally weld discontinuities such as porosities, lack of fusion, and other elongated indications. The AI is used to help detect and classify suspicious discontinuities in the welds to maximize the process quality. However, the final decision to either reject a defect, or accept it with indications or treat it as an AI false positive – all according with ASNT, ISO or other applicable international standards – shall be made by a human expert. We propose a continuously learning AI that follows a transfer learning approach based on a distributed, multi-tenant online cloud infrastructure to collect human feedback and continuously gather knowledge to improve the AI.
By using the AI, a new working platform would be launched and provide remote real-time inspection by all workforce of the industrial professionals. It would reinforce overall work efficiency and quality, will lead further digital transformation by using the data stored in server of the images of DR with the results of interpretation.
Biography
Mr. Teruaki Sano, a Principal QC Engineer at JGC CORPORATION, specializes in metallurgy and welding. His research interests include ensuring the soundness of welds through NDE. He provides consultation on material, welding, and NDE for Oil & Gas and chemical projects more than 15 years. With extensive field QC experience, he troubleshoots welding and inspection issues. Additionally, he actively participates in the Japan Welding Engineering Society and involve in the revision of JIS.
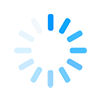