In-Process Ultrasonic Phased Array Inspection for Safety-Critical Components
Tracks
Energy
Tuesday, October 22, 2024 |
4:30 PM - 5:00 PM |
207/208 - Technical Session |
Details
Safety-critical fabrications found in the Nuclear, Defence and Energy sectors often require thick section multi-pass welds when joining multiple components together. Furthermore, they often use welding processes which provide high-deposition rates such as Metal Inert Gas/Metal Active Gas (MIG/MAG) and Submerged Arc Welding (SAW). Traditionally, manufacture and inspection of these welded components are performed as entirely separate processes. This ultimately limits productivity and fabrication throughput along with increasing re-work when defects are detected post-build. Several tangible commercial and economic benefits may be realised by deploying the inspection process at the point of manufacture.
Deploying traditional Phased Array Ultrasonic Testing (PAUT) strategies during welding poses significant technical challenges. Component surface temperatures during welding operations greatly exceed the operating range of traditional contact ultrasonic equipment. Furthermore, the thermal gradients generated by the welding process have significant negative effects on the ultrasound generation, altering the expected sound path and increasing attenuation. A couplant free solution is required to avoid accidentally introducing defects by applying liquid coupling in the region surrounding the active welding process.
Here, dry-coupled Phased Array Ultrasonic Testing (PAUT) is deployed during welding to allow detection of imperfections and flaws at the earliest possible point, thus reducing rework, repair and removing redundant mid-production inspections, delivering high-quality welds right, first time.
The development of this system has required novel approaches to overcome the challenges associated with deployment of PAUT at the point of manufacture. As a result of these innovations, this system is shown to be compatible with a variety of welding processes including Gas Tungsten Arc Welding (GTAW), MIG/MAG and SAW. The results of this work are presented on large-scale plate and pipe demonstrators with controlled intentional defects for process verification and comparison with traditional, post-build PAUT approaches.
Deploying traditional Phased Array Ultrasonic Testing (PAUT) strategies during welding poses significant technical challenges. Component surface temperatures during welding operations greatly exceed the operating range of traditional contact ultrasonic equipment. Furthermore, the thermal gradients generated by the welding process have significant negative effects on the ultrasound generation, altering the expected sound path and increasing attenuation. A couplant free solution is required to avoid accidentally introducing defects by applying liquid coupling in the region surrounding the active welding process.
Here, dry-coupled Phased Array Ultrasonic Testing (PAUT) is deployed during welding to allow detection of imperfections and flaws at the earliest possible point, thus reducing rework, repair and removing redundant mid-production inspections, delivering high-quality welds right, first time.
The development of this system has required novel approaches to overcome the challenges associated with deployment of PAUT at the point of manufacture. As a result of these innovations, this system is shown to be compatible with a variety of welding processes including Gas Tungsten Arc Welding (GTAW), MIG/MAG and SAW. The results of this work are presented on large-scale plate and pipe demonstrators with controlled intentional defects for process verification and comparison with traditional, post-build PAUT approaches.
Speaker
Nina Sweeney
Knowledge Transfer Associate
University Of Strathclyde
In-Process Ultrasonic Phased Array Inspection for Safety-Critical Components
Presentation Description
Safety-critical fabrications found in the Nuclear, Defence and Energy sectors often require thick section multi-pass welds when joining multiple components together. Furthermore, they often use welding processes which provide high-deposition rates such as Metal Inert Gas/Metal Active Gas (MIG/MAG) and Submerged Arc Welding (SAW). Traditionally, manufacture and inspection of these welded components are performed as entirely separate processes. This ultimately limits productivity and fabrication throughput along with increasing re-work when defects are detected post-build. Several tangible commercial and economic benefits may be realised by deploying the inspection process at the point of manufacture.
Deploying traditional Phased Array Ultrasonic Testing (PAUT) strategies during welding poses significant technical challenges. Component surface temperatures during welding operations greatly exceed the operating range of traditional contact ultrasonic equipment. Furthermore, the thermal gradients generated by the welding process have significant negative effects on the ultrasound generation, altering the expected sound path and increasing attenuation. A couplant free solution is required to avoid accidentally introducing defects by applying liquid coupling in the region surrounding the active welding process.
Here, dry-coupled Phased Array Ultrasonic Testing (PAUT) is deployed during welding to allow detection of imperfections and flaws at the earliest possible point, thus reducing rework, repair and removing redundant mid-production inspections, delivering high-quality welds right, first time.
The development of this system has required novel approaches to overcome the challenges associated with deployment of PAUT at the point of manufacture. As a result of these innovations, this system is shown to be compatible with a variety of welding processes including Gas Tungsten Arc Welding (GTAW), MIG/MAG and SAW. The results of this work are presented on large-scale plate and pipe demonstrators with controlled intentional defects for process verification and comparison with traditional, post-build PAUT approaches.
Deploying traditional Phased Array Ultrasonic Testing (PAUT) strategies during welding poses significant technical challenges. Component surface temperatures during welding operations greatly exceed the operating range of traditional contact ultrasonic equipment. Furthermore, the thermal gradients generated by the welding process have significant negative effects on the ultrasound generation, altering the expected sound path and increasing attenuation. A couplant free solution is required to avoid accidentally introducing defects by applying liquid coupling in the region surrounding the active welding process.
Here, dry-coupled Phased Array Ultrasonic Testing (PAUT) is deployed during welding to allow detection of imperfections and flaws at the earliest possible point, thus reducing rework, repair and removing redundant mid-production inspections, delivering high-quality welds right, first time.
The development of this system has required novel approaches to overcome the challenges associated with deployment of PAUT at the point of manufacture. As a result of these innovations, this system is shown to be compatible with a variety of welding processes including Gas Tungsten Arc Welding (GTAW), MIG/MAG and SAW. The results of this work are presented on large-scale plate and pipe demonstrators with controlled intentional defects for process verification and comparison with traditional, post-build PAUT approaches.
Biography
Nina Sweeney recently completed her Engineering Doctorate at the University of Strathclyde sponsored by Peak NDT Ltd. Her EngD looked at the considerations necessary for deployment of in-process ultrasonic inspection and monitoring for fusion welding processes. Post EngD she took a position as a Knowledge Transfer Associate at the University of Strathclyde to further the development and deployment of novel in-process phased array ultrasonic testing techniques.
She holds a PCN Level 2 3.1 and 3.2 in Manual Ultrasonic Testing of Welds and is hoping to further her training to achieve certification for phased array inspection this year.
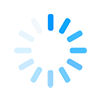