Ultrasonic Total Focusing Method (TFM) for AIRBUS aerospace applications
Tracks
Transportation
Tuesday, October 22, 2024 |
4:00 PM - 4:30 PM |
206 - Short Course & Technical Session |
Details
As the ultrasonic phased array (PAUT) applications and the related equipment became more and more common in aerospace industry, both for large inspection systems in manufacturing as well as portable devices, the latest generation of equipment additionally offers the total focusing method, TFM, based on full matrix capture, FMC.
For an efficient inspection AIRBUS Operations makes use of these options and develops dedicated inspection procedures, both for manufacturing and In-Service applications.
In manufacturing one application for the TFM method is related to the inspection of Additive Manufactured Parts made by Direct Energy Deposition (DED). Due to its dedicated focussing on each pixel of the Region of Interest (ROI) the TFM method enables a significant improvement in detection and sizing of small irregularities in those metallic parts. Furthermore, the entire thickness of the inspection area can be covered without adapting the setup / focussing parameters which leads to an improved and accelerated inspection process.
An example for an In-Service application is the inspection of metallic T-shaped components. The target is to detect fatigue cracks in webs of various configurations in terms of thickness, bore hole diameter and depth, with only one inspection setup. In order to overcome the complexity of failure-prone procedures with many different equipment settings using conventional PAUT technology, the inspector can now inspect these different components and configurations with one equipment setup, thanks to focussing in each pixel of the ROI obtained by TFM reconstruction.
The presentation will give an overview of the TFM technique including relevant examples of its use on different AIRBUS applications.
For an efficient inspection AIRBUS Operations makes use of these options and develops dedicated inspection procedures, both for manufacturing and In-Service applications.
In manufacturing one application for the TFM method is related to the inspection of Additive Manufactured Parts made by Direct Energy Deposition (DED). Due to its dedicated focussing on each pixel of the Region of Interest (ROI) the TFM method enables a significant improvement in detection and sizing of small irregularities in those metallic parts. Furthermore, the entire thickness of the inspection area can be covered without adapting the setup / focussing parameters which leads to an improved and accelerated inspection process.
An example for an In-Service application is the inspection of metallic T-shaped components. The target is to detect fatigue cracks in webs of various configurations in terms of thickness, bore hole diameter and depth, with only one inspection setup. In order to overcome the complexity of failure-prone procedures with many different equipment settings using conventional PAUT technology, the inspector can now inspect these different components and configurations with one equipment setup, thanks to focussing in each pixel of the ROI obtained by TFM reconstruction.
The presentation will give an overview of the TFM technique including relevant examples of its use on different AIRBUS applications.
Speaker
Jens Kethler
Expert NDT in Production
Ultrasonic Total Focusing Method (TFM) for AIRBUS aerospace applications
Presentation Description
As the ultrasonic phased array (PAUT) applications and the related equipment became more and more common in aerospace industry, both for large inspection systems in manufacturing as well as portable devices, the latest generation of equipment additionally offers the total focusing method, TFM, based on full matrix capture, FMC.
For an efficient inspection AIRBUS Operations makes use of these options and develops dedicated inspection procedures, both for manufacturing and In-Service applications.
In manufacturing one application for the TFM method is related to the inspection of Additive Manufactured Parts made by Direct Energy Deposition (DED). Due to its dedicated focussing on each pixel of the Region of Interest (ROI) the TFM method enables a significant improvement in detection and sizing of small irregularities in those metallic parts.
Furthermore, the entire thickness of the inspection area can be covered without adapting the setup / focussing parameters which leads to an improved and accelerated inspection process.
An example for an In-Service application is the inspection of metallic T-shaped components. The target is to detect fatigue cracks in webs of various configurations in terms of thickness, bore hole diameter and depth, with only one inspection setup. In order to overcome the complexity of failure-prone procedures with many different equipment settings using conventional PAUT technology, the inspector can now inspect these different components and configurations with one equipment setup, thanks to focussing in each pixel of the ROI obtained by TFM reconstruction.
The presentation will give an overview of the TFM technique including relevant examples of its use on different AIRBUS applications.
For an efficient inspection AIRBUS Operations makes use of these options and develops dedicated inspection procedures, both for manufacturing and In-Service applications.
In manufacturing one application for the TFM method is related to the inspection of Additive Manufactured Parts made by Direct Energy Deposition (DED). Due to its dedicated focussing on each pixel of the Region of Interest (ROI) the TFM method enables a significant improvement in detection and sizing of small irregularities in those metallic parts.
Furthermore, the entire thickness of the inspection area can be covered without adapting the setup / focussing parameters which leads to an improved and accelerated inspection process.
An example for an In-Service application is the inspection of metallic T-shaped components. The target is to detect fatigue cracks in webs of various configurations in terms of thickness, bore hole diameter and depth, with only one inspection setup. In order to overcome the complexity of failure-prone procedures with many different equipment settings using conventional PAUT technology, the inspector can now inspect these different components and configurations with one equipment setup, thanks to focussing in each pixel of the ROI obtained by TFM reconstruction.
The presentation will give an overview of the TFM technique including relevant examples of its use on different AIRBUS applications.
Biography
Jens Kethler studied Applied Physics at University of Applied Sciences and graduated in 1999 with a diploma thesis about optical profile measurement of laser beam welded aluminum structures. From 1999 to 2001 he worked as scientific engineer at the BIAS Institute in Bremen, Germany. Since 2001 he works as Research/Development Engineer at AIRBUS Operations GmbH in the field of NDT within Materials, Processes & Tests engineering domain. Since 2017 he is an AIRBUS Expert for NDT methods in Production.
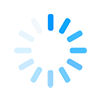