Magnetostrictive Transducers for Guided Wave Testing of Industrial Components
Tracks
NDT Methods
Thursday, October 24, 2024 |
11:00 AM - 11:30 AM |
213/214 - Campfire & Deep Dive |
Details
Over the last two decades, guided wave testing (GWT) has evolved from applications on a limited number of R&D efforts to a well-established field inspection method. The first commercially available guided wave systems were based on both piezoelectric transducers and electromagnetic acoustic transducers (EMATs). In the family of EMATs, the most cost-effective solution for long range testing in carbon steel are magnetostrictive sensors utilizing Joule-Villari or Widemann effects. This technology has been developed by Southwest Research Institute (SwRI) and other organizations since 1998; commercially available instrumentation and software are now widely available.
Today, GWT is mostly considered to be a screening tool for locating damage over a large area for later characterization by other inspection techniques. Even as a screening method, the technology is in high demand for screening of a large number of industrial components, including pipelines, pressure vessels, storage tanks, heat exchanger tubing, steel ropes, ship hulls, anchor rods, and boiler tubes. Aging of these components results in generalized corrosion, cracking, and delamination, creating situations with high attenuation of guided waves. Also, many structural components have high guided wave attenuation even when new, including buried and coated pipes, concrete structures, composite components. To deal with these situations, higher power transducers and instrumentation have been developed worldwide.
Higher power transduction has been accomplished by developing reversed Wiedemann effect magnetostrictive transducers (MsTs) utilizing ferromagnetic ribbons cores. These transducers were first presented at ECNDT 2010, and were recognized with a certificate of innovation. In this presentation, a range of MsT probes with great variety of form factors will be presented, from tiny collars for tubes with diameters less than 0.5 in. to large probes with a segmented array of sensors suitable for inspection of both pipes and plates. Frequency-amplitude characteristics of these probes as a function of magnetization and heat treatment process utilized for ferromagnetic ribbons will be discussed. This discussion will help the audience understand the logic behind specific MsT designs.
The growing number of anomalies in aging components requires enhanced data collection and anomaly imaging protocols. This is the reason why the major trend in development of magnetostrictive transduction systems is higher power transduction and utilization of array sensors with enhanced focusing capability.
An additional topic of discussion will be discussion of a variety of MsT probes with automated data collection function, such as the MsT 360 omnidirectional probe, Linear Scan MsT probe, and MsT 8x8 probe with phased array functionality. The probes come with data acquisition and analysis software allowing mapping of anomalies in rather large structures such as storage tank walls and bottoms, using Full Matrix Capture (FMC) and Total Focusing Method (TFM) reconstruction. Examples of defect imaging in actual storage tanks will be discussed along with projected future directions of technology development.
Today, GWT is mostly considered to be a screening tool for locating damage over a large area for later characterization by other inspection techniques. Even as a screening method, the technology is in high demand for screening of a large number of industrial components, including pipelines, pressure vessels, storage tanks, heat exchanger tubing, steel ropes, ship hulls, anchor rods, and boiler tubes. Aging of these components results in generalized corrosion, cracking, and delamination, creating situations with high attenuation of guided waves. Also, many structural components have high guided wave attenuation even when new, including buried and coated pipes, concrete structures, composite components. To deal with these situations, higher power transducers and instrumentation have been developed worldwide.
Higher power transduction has been accomplished by developing reversed Wiedemann effect magnetostrictive transducers (MsTs) utilizing ferromagnetic ribbons cores. These transducers were first presented at ECNDT 2010, and were recognized with a certificate of innovation. In this presentation, a range of MsT probes with great variety of form factors will be presented, from tiny collars for tubes with diameters less than 0.5 in. to large probes with a segmented array of sensors suitable for inspection of both pipes and plates. Frequency-amplitude characteristics of these probes as a function of magnetization and heat treatment process utilized for ferromagnetic ribbons will be discussed. This discussion will help the audience understand the logic behind specific MsT designs.
The growing number of anomalies in aging components requires enhanced data collection and anomaly imaging protocols. This is the reason why the major trend in development of magnetostrictive transduction systems is higher power transduction and utilization of array sensors with enhanced focusing capability.
An additional topic of discussion will be discussion of a variety of MsT probes with automated data collection function, such as the MsT 360 omnidirectional probe, Linear Scan MsT probe, and MsT 8x8 probe with phased array functionality. The probes come with data acquisition and analysis software allowing mapping of anomalies in rather large structures such as storage tank walls and bottoms, using Full Matrix Capture (FMC) and Total Focusing Method (TFM) reconstruction. Examples of defect imaging in actual storage tanks will be discussed along with projected future directions of technology development.
Speaker
Sergey Vinogradov
Staff Engineer
Southwest Research Institute
Magnetostrictive Transducers for Guided Wave Testing of Industrial Components
Presentation Description
Over the last two decades, guided wave testing (GWT) has evolved from applications on a limited number of R&D efforts to a well-established field inspection method. The first commercially available guided wave systems were based on both piezoelectric transducers and electromagnetic acoustic transducers (EMATs). In the family of EMATs, the most cost-effective solution for long range testing in carbon steel are magnetostrictive sensors utilizing Joule-Villari or Widemann effects. This technology has been developed by Southwest Research Institute (SwRI) and other organizations since 1998; commercially available instrumentation and software are now widely available.
Today, GWT is mostly considered to be a screening tool for locating damage over a large area for later characterization by other inspection techniques. Even as a screening method, the technology is in high demand for screening of a large number of industrial components, including pipelines, pressure vessels, storage tanks, heat exchanger tubing, steel ropes, ship hulls, anchor rods, and boiler tubes. Aging of these components results in generalized corrosion, cracking, and delamination, creating situations with high attenuation of guided waves. Also, many structural components have high guided wave attenuation even when new, including buried and coated pipes, concrete structures, composite components. To deal with these situations, higher power transducers and instrumentation have been developed worldwide.
Higher power transduction has been accomplished by developing reversed Wiedemann effect magnetostrictive transducers (MsTs) utilizing ferromagnetic ribbons cores. These transducers were first presented at ECNDT 2010, and were recognized with a certificate of innovation. In this presentation, a range of MsT probes with great variety of form factors will be presented, from tiny collars for tubes with diameters less than 0.5 in. to large probes with a segmented array of sensors suitable for inspection of both pipes and plates. Frequency-amplitude characteristics of these probes as a function of magnetization and heat treatment process utilized for ferromagnetic ribbons will be discussed. This discussion will help the audience understand the logic behind specific MsT designs.
The growing number of anomalies in aging components requires enhanced data collection and anomaly imaging protocols. This is the reason why the major trend in development of magnetostrictive transduction systems is higher power transduction and utilization of array sensors with enhanced focusing capability.
An additional topic of discussion will be discussion of a variety of MsT probes with automated data collection function, such as the MsT 360 omnidirectional probe, Linear Scan MsT probe, and MsT 8x8 probe with phased array functionality. The probes come with data acquisition and analysis software allowing mapping of anomalies in rather large structures such as storage tank walls and bottoms, using Full Matrix Capture (FMC) and Total Focusing Method (TFM) reconstruction. Examples of defect imaging in actual storage tanks will be discussed along with projected future directions of technology development.
Today, GWT is mostly considered to be a screening tool for locating damage over a large area for later characterization by other inspection techniques. Even as a screening method, the technology is in high demand for screening of a large number of industrial components, including pipelines, pressure vessels, storage tanks, heat exchanger tubing, steel ropes, ship hulls, anchor rods, and boiler tubes. Aging of these components results in generalized corrosion, cracking, and delamination, creating situations with high attenuation of guided waves. Also, many structural components have high guided wave attenuation even when new, including buried and coated pipes, concrete structures, composite components. To deal with these situations, higher power transducers and instrumentation have been developed worldwide.
Higher power transduction has been accomplished by developing reversed Wiedemann effect magnetostrictive transducers (MsTs) utilizing ferromagnetic ribbons cores. These transducers were first presented at ECNDT 2010, and were recognized with a certificate of innovation. In this presentation, a range of MsT probes with great variety of form factors will be presented, from tiny collars for tubes with diameters less than 0.5 in. to large probes with a segmented array of sensors suitable for inspection of both pipes and plates. Frequency-amplitude characteristics of these probes as a function of magnetization and heat treatment process utilized for ferromagnetic ribbons will be discussed. This discussion will help the audience understand the logic behind specific MsT designs.
The growing number of anomalies in aging components requires enhanced data collection and anomaly imaging protocols. This is the reason why the major trend in development of magnetostrictive transduction systems is higher power transduction and utilization of array sensors with enhanced focusing capability.
An additional topic of discussion will be discussion of a variety of MsT probes with automated data collection function, such as the MsT 360 omnidirectional probe, Linear Scan MsT probe, and MsT 8x8 probe with phased array functionality. The probes come with data acquisition and analysis software allowing mapping of anomalies in rather large structures such as storage tank walls and bottoms, using Full Matrix Capture (FMC) and Total Focusing Method (TFM) reconstruction. Examples of defect imaging in actual storage tanks will be discussed along with projected future directions of technology development.
Biography
Dr. Sergey Vinogradov is a Staff Engineer at the Structural Engineering Department of Southwest Research Institute in San Antonio, Texas. He has 34 years of experience in developing of advanced techniques for nondestructive evaluation of materials and structures. Dr. Vinogradov pioneered the high-powered magnetostrictive transducers based on the reversed Wiedemann effect and he is SWRI-certified Level III in guided wave testing methods.
Dr. Vinogradov authored 34 patents and published more than 75 conference and peer to peer reviewed papers in the field of NDE.
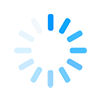