Eddy Current Array improving long products surface inspection capabilities.
Tracks
NDT Methods
Wednesday, October 23, 2024 |
2:00 PM - 2:30 PM |
207/208 - Technical Session |
Details
Surface inspection of long products in the metal manufacturing industry is part of standard inspection requirements. As product quality/variety and performance standards continuously evolve, so do the inspection requirements. Product condition, anywhere from hot rolled to peeled surfaced, are typically analyzed in-line at the different manufacturing stage of this very demanding environment.
Common available inspection methods use rotating principle and aim for primarily elongated flaws (longitudinal). Strong from research and development patents on Eddy current Array, Evident developed a technology approach bases on a nonrotating technique proposing equivalent/greater detectability performance, in an efficient and robust package for ferromagnetic or non-ferromagnetic material with surface condition from hot rolled (black) to peeled products (bright).
The article will illustrate how the evolution from conventional Eddy Current to advanced ECA technology, based on flexible printed circuit board, allows implementation for a broader range of applications. It includes detection principle experimental results using intricate coil patterns on varieties of product geometries, flaws sizes and orientation (not limited to 0deg or 90deg). Thus, an explanation on highspeed dynamic sensitivity correction patents implementation and increased air gap detection effects on overall sensitivity/ stability performances.
Combined, into a new pass-through inspection solution; flexible ECA probes, advanced acquisition features, comprehensive software interface and workflow, brings a new philosophy and approach for long product surface inspection needs.
Common available inspection methods use rotating principle and aim for primarily elongated flaws (longitudinal). Strong from research and development patents on Eddy current Array, Evident developed a technology approach bases on a nonrotating technique proposing equivalent/greater detectability performance, in an efficient and robust package for ferromagnetic or non-ferromagnetic material with surface condition from hot rolled (black) to peeled products (bright).
The article will illustrate how the evolution from conventional Eddy Current to advanced ECA technology, based on flexible printed circuit board, allows implementation for a broader range of applications. It includes detection principle experimental results using intricate coil patterns on varieties of product geometries, flaws sizes and orientation (not limited to 0deg or 90deg). Thus, an explanation on highspeed dynamic sensitivity correction patents implementation and increased air gap detection effects on overall sensitivity/ stability performances.
Combined, into a new pass-through inspection solution; flexible ECA probes, advanced acquisition features, comprehensive software interface and workflow, brings a new philosophy and approach for long product surface inspection needs.
Speaker
Pier Lévesque
Director, Metals Market Development
Evident Scientific
Eddy Current Array improving long products surface inspection capabilities.
Presentation Description
Surface inspection of long products in the metal manufacturing industry is part of standard inspection requirements. As product quality/variety and performance standards continuously evolve, so do the inspection requirements. Product condition, anywhere from hot rolled to peeled surfaced, are typically analyzed in-line at the different manufacturing stage of this very demanding environment.
Common available inspection methods use rotating principle and aim for primarily elongated flaws (longitudinal). Strong from research and development patents on Eddy current Array, Evident developed a technology approach bases on a nonrotating technique proposing equivalent/greater detectability performance, in an efficient and robust package for ferromagnetic or non-ferromagnetic material with surface condition from hot rolled (black) to peeled products (bright).
The article will illustrate how the evolution from conventional Eddy Current to advanced ECA technology, based on flexible printed circuit board, allows implementation for a broader range of applications. It includes detection principle experimental results using intricate coil patterns on varieties of product geometries, flaws sizes and orientation (not limited to 0deg or 90deg). Thus, an explanation on highspeed dynamic sensitivity correction patents implementation and increased air gap detection effects on overall sensitivity/ stability performances.
Combined, into a new pass-through inspection solution; flexible ECA probes, advanced acquisition features, comprehensive software interface and workflow, brings a new philosophy and approach for long product surface inspection needs.
Common available inspection methods use rotating principle and aim for primarily elongated flaws (longitudinal). Strong from research and development patents on Eddy current Array, Evident developed a technology approach bases on a nonrotating technique proposing equivalent/greater detectability performance, in an efficient and robust package for ferromagnetic or non-ferromagnetic material with surface condition from hot rolled (black) to peeled products (bright).
The article will illustrate how the evolution from conventional Eddy Current to advanced ECA technology, based on flexible printed circuit board, allows implementation for a broader range of applications. It includes detection principle experimental results using intricate coil patterns on varieties of product geometries, flaws sizes and orientation (not limited to 0deg or 90deg). Thus, an explanation on highspeed dynamic sensitivity correction patents implementation and increased air gap detection effects on overall sensitivity/ stability performances.
Combined, into a new pass-through inspection solution; flexible ECA probes, advanced acquisition features, comprehensive software interface and workflow, brings a new philosophy and approach for long product surface inspection needs.
Biography
Over 20 years of experience in Non-Destructive Testing (NDT). Following an academic path in science, started as an NDT specialist, participating in the development and installation of a wide variety of NDT system solutions worldwide building expertise and experience. Along the years, held multiples positions including; project management, product line manager for Tube, bar & billet systems and now in a global role as Director for Metals market development.
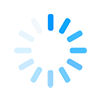