Detection of MicroTextured Regions inside titanium alloys using Ultrasonic Reflection Matrices
Tracks
NDT Methods
Thursday, October 24, 2024 |
9:00 AM - 9:30 AM |
207/208 - Technical Session |
Details
The aim of this work is to develop an approach for the volumetric detection of microtextured regions (MTRs) in titanium alloys using ultrasound.
The study of this type of structure follows the Airbus A380 accident in 2017, in which a ruptured hub led to the aircraft's emergency landing. The BEA report [1] highlights the fact that the origin of the rupture was a MTR, which consist in an extended zone where the microstructure of titanium alloys has a preferred crystallographic orientation. Under certain conditions, stress accumulation at the boundaries of these regions is observed and can lead to a reduction in the mechanical strength of the parts. In particular, a significant reduction in dwell fatigue life can be observed..
Detecting these MTRs is usually done by measuring crystallographic orientation using diffraction methods such as electron backscatter diffraction (EBSD), which provides a local reference measurement but is limited to surface information. As MTRs can be present in the volume of a part, the development of a non-destructive volume inspection method would be an asset for their detection.
Ultrasonic methods are widely used in industry for volume inspection of parts. Within a MTR, the ultrasonic waves speed is anisotropic and depends on the dominant crystallographic orientation [2]. The challenge is thus to determine the angular dependence of the local velocity. The employed approach is inspired by a method developed in the medical field; it uses a multi-element ultrasonic probe to acquire the signal backscattered by the microstructure. It is based on a signal processing algorithm known as the reflection matrix approach [3], which consists in focusing in emission and reception at distinct points of the inspected volume to extract information on the quality of the focus. An estimate of the actual local velocity can be obtained by optimizing the focusing quality with respect to the elastic wave velocity assumption. This method was applied to measurements performed on a Ti64 billet sample at a frequency of 3.5 MHz. The obtained results are a milestone for the eventual measurement of local velocity anisotropy and thus the detection of MTRs. There is no reference method for detecting MTRs in the volume, therefore data are fully simulated to assess the method's performance. As the microstructure is very complex to model, homogenized media are used and point scatterers simulate the source of backscattered noise. In this way, data are generated to simulate structures as closely as possible to the MTRs, with the size, shape and depth required to estimate the detection limit.
[1] BEA, Rapport d’enquête - Accident de l’avion AIRBUS A380-861..
[2] B. Lan et al., Acta Mater. 63, 107–122 (2014).
[3] W. Lambert et al., Phys. Rev. X (2020).
Detecting these MTRs is usually done by measuring crystallographic orientation using diffraction methods such as electron backscatter diffraction (EBSD), which provides a local reference measurement but is limited to surface information. As MTRs can be present in the volume of a part, the development of a non-destructive volume inspection method would be an asset for their detection.
Ultrasonic methods are widely used in industry for volume inspection of parts. Within a MTR, the ultrasonic waves speed is anisotropic and depends on the dominant crystallographic orientation [2]. The challenge is thus to determine the angular dependence of the local velocity. The employed approach is inspired by a method developed in the medical field; it uses a multi-element ultrasonic probe to acquire the signal backscattered by the microstructure. It is based on a signal processing algorithm known as the reflection matrix approach [3], which consists in focusing in emission and reception at distinct points of the inspected volume to extract information on the quality of the focus. An estimate of the actual local velocity can be obtained by optimizing the focusing quality with respect to the elastic wave velocity assumption. This method was applied to measurements performed on a Ti64 billet sample at a frequency of 3.5 MHz. The obtained results are a milestone for the eventual measurement of local velocity anisotropy and thus the detection of MTRs. There is no reference method for detecting MTRs in the volume, therefore data are fully simulated to assess the method's performance. As the microstructure is very complex to model, homogenized media are used and point scatterers simulate the source of backscattered noise. In this way, data are generated to simulate structures as closely as possible to the MTRs, with the size, shape and depth required to estimate the detection limit.
[1] BEA, Rapport d’enquête - Accident de l’avion AIRBUS A380-861..
[2] B. Lan et al., Acta Mater. 63, 107–122 (2014).
[3] W. Lambert et al., Phys. Rev. X (2020).
Speaker
Mr Gatien CLEMENT
PhD Student
Detection of MicroTextured Regions inside titanium alloys using Ultrasonic Reflection Matrices
Presentation Description
The aim of this work is to develop an approach for the volumetric detection of microtextured regions (MTRs) in titanium alloys using ultrasound.
The study of this type of structure follows the Airbus A380 accident in 2017, in which a ruptured hub led to the aircraft's emergency landing. The BEA report [1] highlights the fact that the origin of the rupture was a MTR, which consist in an extended zone where the microstructure of titanium alloys has a preferred crystallographic orientation. Under certain conditions, stress accumulation at the boundaries of these regions is observed and can lead to a reduction in the mechanical strength of the parts. In particular, a significant reduction in dwell fatigue life can be observed.
Detecting these MTRs is usually done by measuring crystallographic orientation using diffraction methods such as electron backscatter diffraction (EBSD), which provides a local reference measurement but is limited to surface information. As MTRs can be present in the volume of a part, the development of a non-destructive volume inspection method would be an asset for their detection.
Ultrasonic methods are widely used in industry for volume inspection of parts. Within a MTR, the ultrasonic waves speed is anisotropic and depends on the dominant crystallographic orientation [2]. The challenge is thus to determine the angular dependence of the local velocity. The employed approach is inspired by a method developed in the medical field; it uses a multi-element ultrasonic probe to acquire the signal backscattered by the microstructure. It is based on a signal processing algorithm known as the reflection matrix approach [3], which consists in focusing in emission and reception at distinct points of the inspected volume to extract information on the quality of the focus. An estimate of the actual local velocity can be obtained by optimizing the focusing quality with respect to the elastic wave velocity assumption. This method was applied to measurements performed on a Ti64 billet sample at a frequency of 3.5 MHz. The obtained results are a milestone for the eventual measurement of local velocity anisotropy and thus the detection of MTRs.
There is no reference method for detecting MTRs in the volume, therefore data are fully simulated to assess the method's performance. As the microstructure is very complex to model, homogenized media are used and point scatterers simulate the source of backscattered noise. In this way, data are generated to simulate structures as closely as possible to the MTRs, with the size, shape and depth required to estimate the detection limit.
[1] BEA, Rapport d’enquête - Accident de l’avion AIRBUS A380-861.
[2] B. Lan et al., Acta Mater. 63, 107–122 (2014).
[3] W. Lambert et al., Phys. Rev. X (2020).
The study of this type of structure follows the Airbus A380 accident in 2017, in which a ruptured hub led to the aircraft's emergency landing. The BEA report [1] highlights the fact that the origin of the rupture was a MTR, which consist in an extended zone where the microstructure of titanium alloys has a preferred crystallographic orientation. Under certain conditions, stress accumulation at the boundaries of these regions is observed and can lead to a reduction in the mechanical strength of the parts. In particular, a significant reduction in dwell fatigue life can be observed.
Detecting these MTRs is usually done by measuring crystallographic orientation using diffraction methods such as electron backscatter diffraction (EBSD), which provides a local reference measurement but is limited to surface information. As MTRs can be present in the volume of a part, the development of a non-destructive volume inspection method would be an asset for their detection.
Ultrasonic methods are widely used in industry for volume inspection of parts. Within a MTR, the ultrasonic waves speed is anisotropic and depends on the dominant crystallographic orientation [2]. The challenge is thus to determine the angular dependence of the local velocity. The employed approach is inspired by a method developed in the medical field; it uses a multi-element ultrasonic probe to acquire the signal backscattered by the microstructure. It is based on a signal processing algorithm known as the reflection matrix approach [3], which consists in focusing in emission and reception at distinct points of the inspected volume to extract information on the quality of the focus. An estimate of the actual local velocity can be obtained by optimizing the focusing quality with respect to the elastic wave velocity assumption. This method was applied to measurements performed on a Ti64 billet sample at a frequency of 3.5 MHz. The obtained results are a milestone for the eventual measurement of local velocity anisotropy and thus the detection of MTRs.
There is no reference method for detecting MTRs in the volume, therefore data are fully simulated to assess the method's performance. As the microstructure is very complex to model, homogenized media are used and point scatterers simulate the source of backscattered noise. In this way, data are generated to simulate structures as closely as possible to the MTRs, with the size, shape and depth required to estimate the detection limit.
[1] BEA, Rapport d’enquête - Accident de l’avion AIRBUS A380-861.
[2] B. Lan et al., Acta Mater. 63, 107–122 (2014).
[3] W. Lambert et al., Phys. Rev. X (2020).
Biography
PhD student in acoustics at Safran Tech and Langevin Institute.
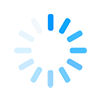