True Pulse-Echo Measurements with Single-Sided Air-Coupled Laser-Excited Ultrasound
Tracks
NDT Methods
Tuesday, October 22, 2024 |
2:00 PM - 2:30 PM |
207/208 - Technical Session |
Details
In ultrasonic testing (UT), single-sided access inspection is required for various applications. Typically, a pulse-echo mode is favored over guided wave or pitch-catch. Measuring the ultrasound echo provides the crucial benefit of enabling accurate defect imaging at true-to-size dimensions and precise defect depth determination.
Traditionally, ultrasonic pulse-echo testing relies on liquid-coupled piezoelectric transducers. However, liquid coupling is sometimes undesirable as it can compromise materials such as composites, and contact-based UT technologies are challenging to automate, especially if the sample geometry is complex or the space is confined, or if the sample is simply not supposed to get in contact with water.
In response, air-coupled UT using piezoelectric transducers has been suggested as a contact-free alternative. However, achieving a pulse-echo mode is typically unattainable with such a setup due to the low sensitivity caused by the significant solid-air impedance mismatch, the low frequency bandwidth and center frequencies, resulting in extended pulse durations and dead zones, and the difficulties in isolating backwall echo signals from surface reflections. Consequently, air-coupled UT is traditionally employed in a pitch-catch mode for single-sided setups. With such a configuration, so-called guided waves (Lamb, Rayleigh) are measured, leading to limited defect resolution and resulting in unwanted defect size distortion. In contrast, in conventional laser UT, a detection laser is directed on the sample surface with allows contact-free pulse-echo measurements. However, this detection laser needs to be very carefully aligned with the sample surface and can not be used for rough surfaces or complex geometries.
In this presentation, we will present a setup termed laser-excited acoustics (LEA) which overcomes the limitations of conventional air-coupled methods, at the same time allowing to scan complex geometries and rough surfaces. For the first time, we introduce a high-resolution air-coupled true pulse-echo method that enables true-to-size imaging of defects such as delamination in composite structures. Our setup comprises a laser for ultrasound excitation and a broadband optical microphone as the air-coupled receiver. By using a pulsed laser, different wave modes are excited, which can be detected as leaky signals in the air using the optical microphone based on refractive index changes in air. This talk will 1) explore the different wave modes generated by laser excitation, 2) introduce the groundbreaking pulse-echo measurement methodology, and 3) present scan results of samples measured in pulse-echo configuration using no gel or water, including industrial setup results.
Traditionally, ultrasonic pulse-echo testing relies on liquid-coupled piezoelectric transducers. However, liquid coupling is sometimes undesirable as it can compromise materials such as composites, and contact-based UT technologies are challenging to automate, especially if the sample geometry is complex or the space is confined, or if the sample is simply not supposed to get in contact with water.
In response, air-coupled UT using piezoelectric transducers has been suggested as a contact-free alternative. However, achieving a pulse-echo mode is typically unattainable with such a setup due to the low sensitivity caused by the significant solid-air impedance mismatch, the low frequency bandwidth and center frequencies, resulting in extended pulse durations and dead zones, and the difficulties in isolating backwall echo signals from surface reflections. Consequently, air-coupled UT is traditionally employed in a pitch-catch mode for single-sided setups. With such a configuration, so-called guided waves (Lamb, Rayleigh) are measured, leading to limited defect resolution and resulting in unwanted defect size distortion. In contrast, in conventional laser UT, a detection laser is directed on the sample surface with allows contact-free pulse-echo measurements. However, this detection laser needs to be very carefully aligned with the sample surface and can not be used for rough surfaces or complex geometries.
In this presentation, we will present a setup termed laser-excited acoustics (LEA) which overcomes the limitations of conventional air-coupled methods, at the same time allowing to scan complex geometries and rough surfaces. For the first time, we introduce a high-resolution air-coupled true pulse-echo method that enables true-to-size imaging of defects such as delamination in composite structures. Our setup comprises a laser for ultrasound excitation and a broadband optical microphone as the air-coupled receiver. By using a pulsed laser, different wave modes are excited, which can be detected as leaky signals in the air using the optical microphone based on refractive index changes in air. This talk will 1) explore the different wave modes generated by laser excitation, 2) introduce the groundbreaking pulse-echo measurement methodology, and 3) present scan results of samples measured in pulse-echo configuration using no gel or water, including industrial setup results.
Speaker
Tobias Hoetzer
True Pulse-Echo Measurements with Single-Sided Air-Coupled Laser-Excited Ultrasound
Presentation Description
In ultrasonic testing (UT), single-sided access inspection is required for various applications. Typically, a pulse-echo mode is favored over guided wave or pitch-catch. Measuring the ultrasound echo provides the crucial benefit of enabling accurate defect imaging at true-to-size dimensions and precise defect depth determination.
Traditionally, ultrasonic pulse-echo testing relies on liquid-coupled piezoelectric transducers. However, liquid coupling is sometimes undesirable as it can compromise materials such as composites, and contact-based UT technologies are challenging to automate, especially if the sample geometry is complex or the space is confined, or if the sample is simply not supposed to get in contact with water.
In response, air-coupled UT using piezoelectric transducers has been suggested as a contact-free alternative. However, achieving a pulse-echo mode is typically unattainable with such a setup due to the low sensitivity caused by the significant solid-air impedance mismatch, the low frequency bandwidth and center frequencies, resulting in extended pulse durations and dead zones, and the difficulties in isolating backwall echo signals from surface reflections. Consequently, air-coupled UT is traditionally employed in a pitch-catch mode for single-sided setups. With such a configuration, so-called guided waves (Lamb, Rayleigh) are measured, leading to limited defect resolution and resulting in unwanted defect size distortion.
In contrast, in conventional laser UT, a detection laser is directed on the sample surface with allows contact-free pulse-echo measurements. However, this detection laser needs to be very carefully aligned with the sample surface and can not be used for rough surfaces or complex geometries.
In this presentation, we will present a setup termed laser-excited acoustics (LEA) which overcomes the limitations of conventional air-coupled methods, at the same time allowing to scan complex geometries and rough surfaces. For the first time, we introduce a high-resolution air-coupled true pulse-echo method that enables true-to-size imaging of defects such as delamination in composite structures. Our setup comprises a laser for ultrasound excitation and a broadband optical microphone as the air-coupled receiver. By using a pulsed laser, different wave modes are excited, which can be detected as leaky signals in the air using the optical microphone based on refractive index changes in air. This talk will 1) explore the different wave modes generated by laser excitation, 2) introduce the groundbreaking pulse-echo measurement methodology, and 3) present scan results of samples measured in pulse-echo configuration using no gel or water, including industrial setup results.
Traditionally, ultrasonic pulse-echo testing relies on liquid-coupled piezoelectric transducers. However, liquid coupling is sometimes undesirable as it can compromise materials such as composites, and contact-based UT technologies are challenging to automate, especially if the sample geometry is complex or the space is confined, or if the sample is simply not supposed to get in contact with water.
In response, air-coupled UT using piezoelectric transducers has been suggested as a contact-free alternative. However, achieving a pulse-echo mode is typically unattainable with such a setup due to the low sensitivity caused by the significant solid-air impedance mismatch, the low frequency bandwidth and center frequencies, resulting in extended pulse durations and dead zones, and the difficulties in isolating backwall echo signals from surface reflections. Consequently, air-coupled UT is traditionally employed in a pitch-catch mode for single-sided setups. With such a configuration, so-called guided waves (Lamb, Rayleigh) are measured, leading to limited defect resolution and resulting in unwanted defect size distortion.
In contrast, in conventional laser UT, a detection laser is directed on the sample surface with allows contact-free pulse-echo measurements. However, this detection laser needs to be very carefully aligned with the sample surface and can not be used for rough surfaces or complex geometries.
In this presentation, we will present a setup termed laser-excited acoustics (LEA) which overcomes the limitations of conventional air-coupled methods, at the same time allowing to scan complex geometries and rough surfaces. For the first time, we introduce a high-resolution air-coupled true pulse-echo method that enables true-to-size imaging of defects such as delamination in composite structures. Our setup comprises a laser for ultrasound excitation and a broadband optical microphone as the air-coupled receiver. By using a pulsed laser, different wave modes are excited, which can be detected as leaky signals in the air using the optical microphone based on refractive index changes in air. This talk will 1) explore the different wave modes generated by laser excitation, 2) introduce the groundbreaking pulse-echo measurement methodology, and 3) present scan results of samples measured in pulse-echo configuration using no gel or water, including industrial setup results.
Biography
Tobias Hötzer is a Senior Project Manager at Xarion Laser Acoustics. Following the completion of his Master's studies in Mechanical Engineering, he went on to work at Xarion in the application development. Presently, Tobias manages projects implementing automated inspection systems for the automotive and aerospace industries, utilizing Xarion's contact-free ultrasonic testing technology.
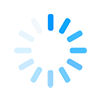