Enhanced C-Scan and 3D views applied to the Inspection of CFRP and GFRP by using Matrix UT probes.
Tracks
Transportation
Thursday, October 24, 2024 |
8:30 AM - 9:00 AM |
213/214 - Campfire & Deep Dive |
Details
Carbon fiber reinforced plastic (CFRP) and glass fiber reinforced plastic (GFRP) are very challenging materials to inspect using ultrasonic methods. Sound attenuation, anisotropy, and complex geometries are some of the challenges to overcome. These materials are predominantly used in the aerospace and wind power generation industries, in components such as panels, blades, and wings, to name a few examples. The most common defects include unbonds, porosity, cracks, delamination, and voids. Under certain conditions, it is nearly impossible to properly assess defects to identify their size, geometry, and location within a part.
Generally, A-scan and B-scan views are available in real-time during the inspection, but they do not provide comprehensive information to technicians. C-scans are available on some instruments but usually not in real-time; they are commonly available in post-analysis software. This delay requires more time to provide crucial information from NDT technicians to decision-makers, like customers or OEMs, to make appropriate repairs or rebuilds.
In the aerospace and wind power generation industries, sizing defects is critical because it affects downtime for repairs. The quicker a technician can obtain complete UT data, the faster they can decide on the next steps. By having a live C-scan and a 3D characterization view of what is underneath the UT probe, technicians can size and characterize defects more confidently. This is especially important for CFRP and GFRP parts, where geometry and size are crucial for assessments.
To provide live C-scan and 3D views, Dolphitech has designed a matrix UT probe that provides real-time UT data. The C-scan offers a top view of the part, presented in two different ways: Time of Flight (TOF) and Amplitude (%). Additionally, the Dolphicam2 offers a 3D view of the C-scan. With these real-time views, technicians can size defects like cracks and impact damages with higher precision compared to zero-degree inspections with conventional elements or linear arrays. This enables technicians to provide a better understanding and assessment of defects to customers, based on high-definition images, compared to conventional A-scan or B-scan methods.
Generally, A-scan and B-scan views are available in real-time during the inspection, but they do not provide comprehensive information to technicians. C-scans are available on some instruments but usually not in real-time; they are commonly available in post-analysis software. This delay requires more time to provide crucial information from NDT technicians to decision-makers, like customers or OEMs, to make appropriate repairs or rebuilds.
In the aerospace and wind power generation industries, sizing defects is critical because it affects downtime for repairs. The quicker a technician can obtain complete UT data, the faster they can decide on the next steps. By having a live C-scan and a 3D characterization view of what is underneath the UT probe, technicians can size and characterize defects more confidently. This is especially important for CFRP and GFRP parts, where geometry and size are crucial for assessments.
To provide live C-scan and 3D views, Dolphitech has designed a matrix UT probe that provides real-time UT data. The C-scan offers a top view of the part, presented in two different ways: Time of Flight (TOF) and Amplitude (%). Additionally, the Dolphicam2 offers a 3D view of the C-scan. With these real-time views, technicians can size defects like cracks and impact damages with higher precision compared to zero-degree inspections with conventional elements or linear arrays. This enables technicians to provide a better understanding and assessment of defects to customers, based on high-definition images, compared to conventional A-scan or B-scan methods.
Speaker
Renato Nogueira
Applications Specialist
Dolphitech
Enhanced C-Scan and 3D views applied to the Inspection of CFRP and GFRP by using Matrix UT probes.
Presentation Description
Carbon fiber reinforced plastic (CFRP) and glass fiber reinforced plastic (GFRP) are very challenging materials to inspect using ultrasonic methods. Sound attenuation, anisotropy, and complex geometries are some of the challenges to overcome. These materials are predominantly used in the aerospace and wind power generation industries, in components such as panels, blades, and wings, to name a few examples. The most common defects include unbonds, porosity, cracks, delamination, and voids. Under certain conditions, it is nearly impossible to properly assess defects to identify their size, geometry, and location within a part.
Generally, A-scan and B-scan views are available in real-time during the inspection, but they do not provide comprehensive information to technicians. C-scans are available on some instruments but usually not in real-time; they are commonly available in post-analysis software. This delay requires more time to provide crucial information from NDT technicians to decision-makers, like customers or OEMs, to make appropriate repairs or rebuilds.
In the aerospace and wind power generation industries, sizing defects is critical because it affects downtime for repairs. The quicker a technician can obtain complete UT data, the faster they can decide on the next steps. By having a live C-scan and a 3D characterization view of what is underneath the UT probe, technicians can size and characterize defects more confidently. This is especially important for CFRP and GFRP parts, where geometry and size are crucial for assessments.
To provide live C-scan and 3D views, Dolphitech has designed a matrix UT probe that provides real-time UT data. The C-scan offers a top view of the part, presented in two different ways: Time of Flight (TOF) and Amplitude (%). Additionally, the Dolphicam2 offers a 3D view of the C-scan. With these real-time views, technicians can size defects like cracks and impact damages with higher precision compared to zero-degree inspections with conventional elements or linear arrays. This enables technicians to provide a better understanding and assessment of defects to customers, based on high-definition images, compared to conventional A-scan or B-scan methods.
Generally, A-scan and B-scan views are available in real-time during the inspection, but they do not provide comprehensive information to technicians. C-scans are available on some instruments but usually not in real-time; they are commonly available in post-analysis software. This delay requires more time to provide crucial information from NDT technicians to decision-makers, like customers or OEMs, to make appropriate repairs or rebuilds.
In the aerospace and wind power generation industries, sizing defects is critical because it affects downtime for repairs. The quicker a technician can obtain complete UT data, the faster they can decide on the next steps. By having a live C-scan and a 3D characterization view of what is underneath the UT probe, technicians can size and characterize defects more confidently. This is especially important for CFRP and GFRP parts, where geometry and size are crucial for assessments.
To provide live C-scan and 3D views, Dolphitech has designed a matrix UT probe that provides real-time UT data. The C-scan offers a top view of the part, presented in two different ways: Time of Flight (TOF) and Amplitude (%). Additionally, the Dolphicam2 offers a 3D view of the C-scan. With these real-time views, technicians can size defects like cracks and impact damages with higher precision compared to zero-degree inspections with conventional elements or linear arrays. This enables technicians to provide a better understanding and assessment of defects to customers, based on high-definition images, compared to conventional A-scan or B-scan methods.
Biography
Bachelor degree in Applied Physics. Certified as level 3 on UT and MFL. 20 years of experience on multiple NDT methods.
Holds a position as applications specialist at Dolphitech, to support customers and distributors located in North and Latin America. Co-author of Full Matrix Capture Training Manual promoted by ASME.
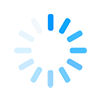