Safe & Digitalized Inspection Through Online Corrosion Monitoring of High Temperature Assets
Tracks
Energy
Thursday, October 24, 2024 |
9:00 AM - 9:30 AM |
213/214 - Campfire & Deep Dive |
Details
To mitigate the imminent future corrosion threats in processing and refining facilities part of Oil, Gas & Petrochemical Industries, a well-structured & digitalized OSI Management program is the need for the industry alignment with IR 4.0 and digitalization of inspection methodology and data acquisition. The planned use of permanently installed sensors for continuous structural health monitoring on critical assets is a must, which will provide facilities with a possibility of proactive decision making and minimizing operation costs and reduce the possibilities of unplanned shutdowns.
Speaker
Mr Mosa Alzahrani
Engineer
Saudi ARAMCO
Safe & Digitalized Inspection Through Online Corrosion Monitoring of High Temperature Assets
9:00 AM - 9:30 AMPresentation Description
To mitigate the imminent future corrosion threats in processing and refining facilities part of Oil, Gas & Petrochemical Industries, a well-structured & digitalized OSI Management program is the need for the industry alignment with IR 4.0 and digitalization of inspection methodology and data acquisition. The planned use of permanently installed sensors for continuous structural health monitoring on critical assets is a must, which will provide facilities with a possibility of proactive decision making and minimizing operation costs and reduce the possibilities of unplanned shutdowns.
In Oil & Energy industry, the corrosion threats are imminent, with severity depends on crude impurities, processing chemical and varying process conditions, such as pressure, temperature and other atmospheric constraints. The periodical inspection on equipment and engineering assets requires accessibility to inspectors, where most facilities and operators spend huge resources on scaffolding, insulation removal, rope access teams, transportation, access permits and even scheduling of skilled inspection technicians. Many of these assets are difficult to reach for inspection, due to a variety of associated safety hazards, i.e. extreme temperatures in the nearby assets, presence of highly combustible products, toxic or acidic vapors, and the presence of radiations. Often times, these constraints, not just increase the cost of inspection, but also increase the health and safety risk to inspection personnel.
For continuously assessing the integrity and usefulness of asset to maintain pressure boundaries, manual ultrasonic wall thinning measurements are being relied upon, whereas the method is time consuming with associated challenges of measurement consistency and data quality. Inspection personnel, often require follow-up field visits due to data inconsistencies, or to seek expert guidance for complex processes and corrosion damage mechanisms, which often rely on estimation and approximation.
The industry, with a focus on digitalization, is increasing the use of permanently installed wireless capable wall thinning measurement ultrasonic sensors. The approach is helping industry to move away from conventional inspection methods towards adopting monitoring philosophy with an initial focus on critical locations. The use of wireless capable wall thinning measurement UT sensors for high temperature equipment allow facilities with an inspection option that is more reliable, and devoid of inspector subjectivity, minimum to zero logistic expenses associated to securing permits & training manpower, erecting scaffolds and the availability of special PPE to enter hazardous locations.
The concept of permanently installed sensors for monitoring wall thinning is not new for Aramco. Inspection Department embarked on this journey since 2009, when a patent for “High Pression Corrosion Monitoring” sensors was granted from US Patent Office. This was the beginning, and till now (i.e. 2021), Inspection Department has evaluated, piloted, approved and deployed several technologies aimed at different operation constraints for diverse operation needs, but with the same objective, i.e. Online Corrosion Monitoring.
The presentation, will provide an overview of different OCM Technologies that are successfully piloted or in the process of being approved. The discussion will focus on providing the participants of the forum, a clear understanding of OCM technologies trialed or approved by Inspection Department, their classification and applications for different operation needs with regards to corrosion classes, operating temperatures, online or on-demand data collection, etc. The aim is to inform the attendees on a full spectrum of ID approved or reviewed OCM Technologies.
In Oil & Energy industry, the corrosion threats are imminent, with severity depends on crude impurities, processing chemical and varying process conditions, such as pressure, temperature and other atmospheric constraints. The periodical inspection on equipment and engineering assets requires accessibility to inspectors, where most facilities and operators spend huge resources on scaffolding, insulation removal, rope access teams, transportation, access permits and even scheduling of skilled inspection technicians. Many of these assets are difficult to reach for inspection, due to a variety of associated safety hazards, i.e. extreme temperatures in the nearby assets, presence of highly combustible products, toxic or acidic vapors, and the presence of radiations. Often times, these constraints, not just increase the cost of inspection, but also increase the health and safety risk to inspection personnel.
For continuously assessing the integrity and usefulness of asset to maintain pressure boundaries, manual ultrasonic wall thinning measurements are being relied upon, whereas the method is time consuming with associated challenges of measurement consistency and data quality. Inspection personnel, often require follow-up field visits due to data inconsistencies, or to seek expert guidance for complex processes and corrosion damage mechanisms, which often rely on estimation and approximation.
The industry, with a focus on digitalization, is increasing the use of permanently installed wireless capable wall thinning measurement ultrasonic sensors. The approach is helping industry to move away from conventional inspection methods towards adopting monitoring philosophy with an initial focus on critical locations. The use of wireless capable wall thinning measurement UT sensors for high temperature equipment allow facilities with an inspection option that is more reliable, and devoid of inspector subjectivity, minimum to zero logistic expenses associated to securing permits & training manpower, erecting scaffolds and the availability of special PPE to enter hazardous locations.
The concept of permanently installed sensors for monitoring wall thinning is not new for Aramco. Inspection Department embarked on this journey since 2009, when a patent for “High Pression Corrosion Monitoring” sensors was granted from US Patent Office. This was the beginning, and till now (i.e. 2021), Inspection Department has evaluated, piloted, approved and deployed several technologies aimed at different operation constraints for diverse operation needs, but with the same objective, i.e. Online Corrosion Monitoring.
The presentation, will provide an overview of different OCM Technologies that are successfully piloted or in the process of being approved. The discussion will focus on providing the participants of the forum, a clear understanding of OCM technologies trialed or approved by Inspection Department, their classification and applications for different operation needs with regards to corrosion classes, operating temperatures, online or on-demand data collection, etc. The aim is to inform the attendees on a full spectrum of ID approved or reviewed OCM Technologies.
Biography
Mosa Alzahrani is an Inspection Technology Engineer Graduated form King Fahd University of Petrolum and Menerals with Bachelour Degree in Mechanical Engineering. Mosa has diverse experiance in the inspection and projects field. Mosa curently is Inspection Technology Engineer at Saudi Aramco-Inpection Department working mainly on scouting, adopting and evaluating new and cutting-edge NDT Inspection Technologies for mass deployment within Saudi Aramco Facilities.
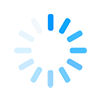